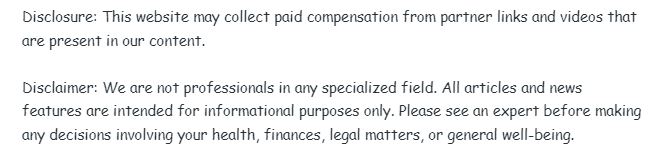
Mill liners are critical components in the mining and mineral processing industries, protecting mill shells from wear and ensuring efficient grinding operations. Regular inspection of mill liners is essential to maintain optimal performance and prevent unexpected breakdowns. But how exactly are these inspections carried out?
Wondering how to inspect mill liners? The inspection process typically begins with a thorough visual examination. Inspectors look for signs of wear, such as cracks, chips, or other damage on the liner surfaces.
They also check for loose bolts or any unusual deformations that could indicate underlying issues.
Next, more detailed methods are employed. Ultrasonic testing is commonly used to measure the thickness of the liners. This non-destructive technique involves sending ultrasonic waves through the material to detect thinning areas that might not be visible to the naked eye. Consistent thickness measurements help determine the wear rate and predict when replacements might be needed.
In addition to ultrasonic testing, magnetic particle inspection can be used to identify surface and slightly subsurface cracks. This method involves applying a magnetic field to the liners and then using magnetic particles to reveal defects. It’s particularly effective for finding small cracks that could lead to larger issues if left untreated.
Finally, professionals who know how to inspect mill liners often use specialized software to log their findings and generate reports. These reports provide valuable insights into the condition of the liners, enabling maintenance teams to plan and execute timely interventions.