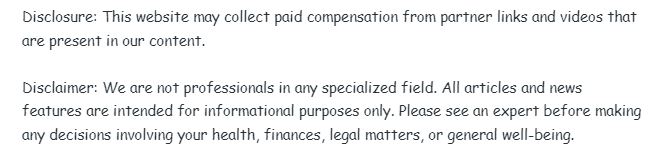
Torque sensor units are designed to operate in a wide temperature range of negative 452 degrees Fahrenheit to positive 450 degrees Fahrenheit. Though there are plenty of uses for these sensor items, in recent years, robotics have relied tremendously on torque sensors and other innovative technologies. Because while most people image robots like those featured on television shows and cartoons, the vast majority of robots exist in factories, particularly in the automotive industry.
According to Robotics Industry Insights, force and tactile sensors are enabling robots to manipulate objects in less-structured environments with greater accuracy and sensitivity.
Most robots designed for collaborative applications already have built-in force and torque sensing capabilities for safety, especially when working alongside humans. With the exploration of these force and tactile sensors, however, robots are better able to perform dangerous tasks that human workers should avoid.
Soon, thanks to this new sensing technology, robots will actually be able to “feel” what they come in contact with. As the robotics sector continues to innovate, more and more industries will start utilizing these machines than ever before. For instance, the construction industry currently has more than 650,000 employers and over 6 million employees, creating nearly $1 trillion worth of manmade structures each year. Since these powerful robots can now see, feel, and even adapt, they can make it much easier to build all sorts of structures and access otherwise impossible-to-reach areas.
“There aren’t many major manufacturing facilities in the world where you’re not going to find a vision system,” said Ian Stern, Product Manager of Force and Torque Sensors at ATI Industrial Automation Apex. “That’s where force sensing is headed. As we start to automate jobs that require that sense of touch, force sensing will become as prevalent as vision.”
Vision technology has already broken into the robotics industry, and it seems as though robotic touch sensing will soon follow suit.
Additionally, Robotics and Automation adds that Universal Robots is planning on showcasing its brand-new e-Series collaborative robot for the first time in the United States at the IMTS industrial technology event.
The new e-Series sets a new standard for collaborative robotics, adding in a built-in force and torque sensing capability, as well as innovative safety features and improved precision.
“As manufacturers increasingly embrace cobots (computer-controlled robot devices), we see the need to support even more demanding applications with the greater accuracy and tool integration of the e-Series,” added Stuart Shepherd, regional sales director for Universal Robots’ American region.
Whether it’s a smalltime shop or a large construction organization, the future will likely see many more robots across the commercial sector.
“The global cobot market is the fastest-growing segment of industrial automation,” added Shepherd.